Electric Discharge Machine
What is Electric Discharge Machining process?
Electric Discharge Machining (EDM) process is also known as spark erosion machining. The principle of metal removal is instantaneous melting and vaporization of the material. Through EDM, tool shape can be replicate on the workpiece material. This process can machine any conductive material regardless of their hardness. The tool and workpiece material were acts as two electrodes, and is separated by a machining gap with dielectric fluid. High volage in the range of 100 V to 400 V is applied between the tool and the workpiece. Material is removed from the workpiece through the occurrence of series of sparks generated between the two electrodes, therefore the spark energy generated erodes the material. Fig. 1 shows the fabrication of micro-hole through EDM process. The EDM process will machine only conducting materials.
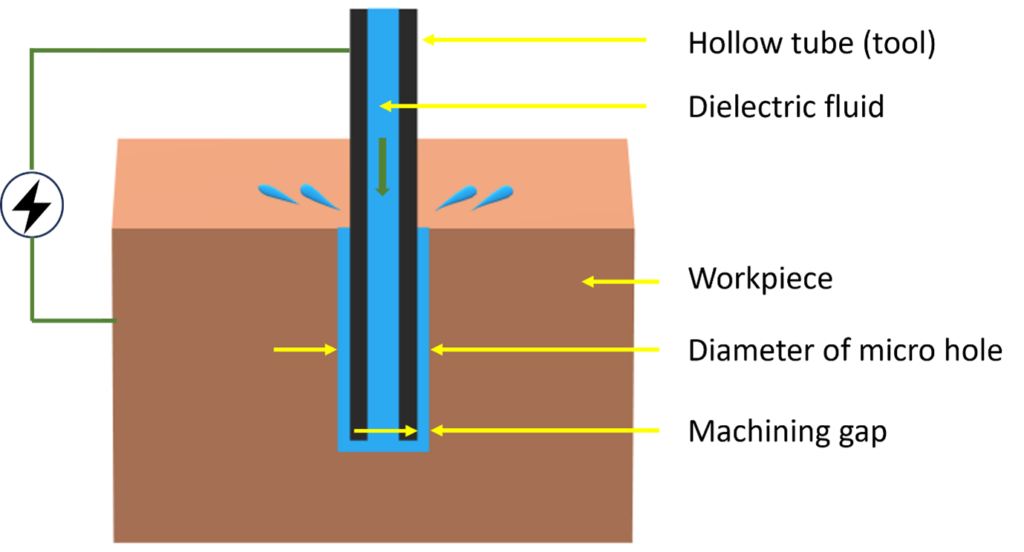
What are the different types of EDM?
There are 3 basic configurations of EDM machining, and they are wire EDM, die sinking EDM, and EDM hole drilling. In this process the material removal takes place by discharging the thermal energy and they are different based on the shape and size of the machining area. In wire EDM, the wire moves in a user predefined path and the material will cut as per the requirements. The die sinking EDM replicate the shape of the tool on the conductive workpiece material. EDM hole drilling is used to drill holes ranging from diameter 0.3 mm to 3mm in thick metal plate, the thickness can go as deep as 200mm.
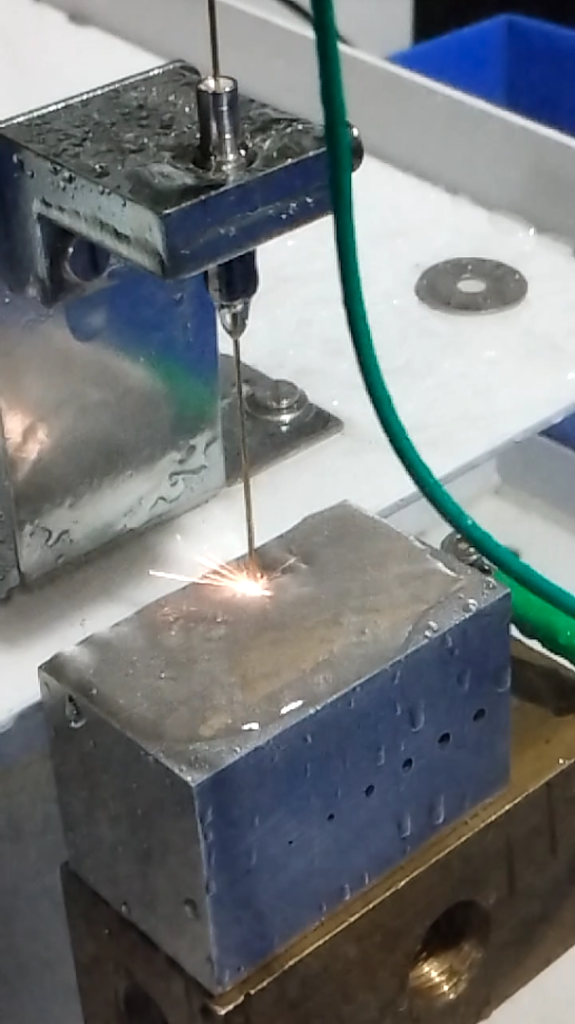
Electric Discharge Machine HX100
Here we are the solution, HEXON INSTRUMENTS PVT LTD., presents HEXON EDM drilling machine.
HEXON Electric discharge Machine Offers Fabrication of Superior Precise Micro Holes across a wide range of materials. We Provide Affordable Solution to produce good quality small holes. We offer customization in EDM Drill As per user requirements.
EDM HX100
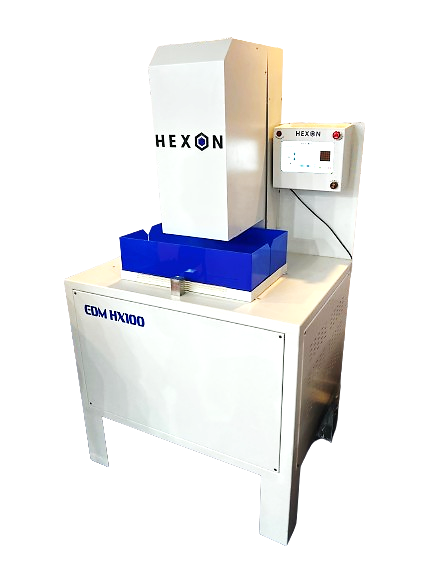
Applications
1. Fabrication of precise micro-holes
Through micro-holes with different diameter size has been fabricated on hard-to-cut alloys. The micro-holes with diameters of around 175 um, 210 um, 360 um and 375 um has been successfully fabricated as shown below. The EDM has capability to produce even less than the mentioned diameters of micro-holes.
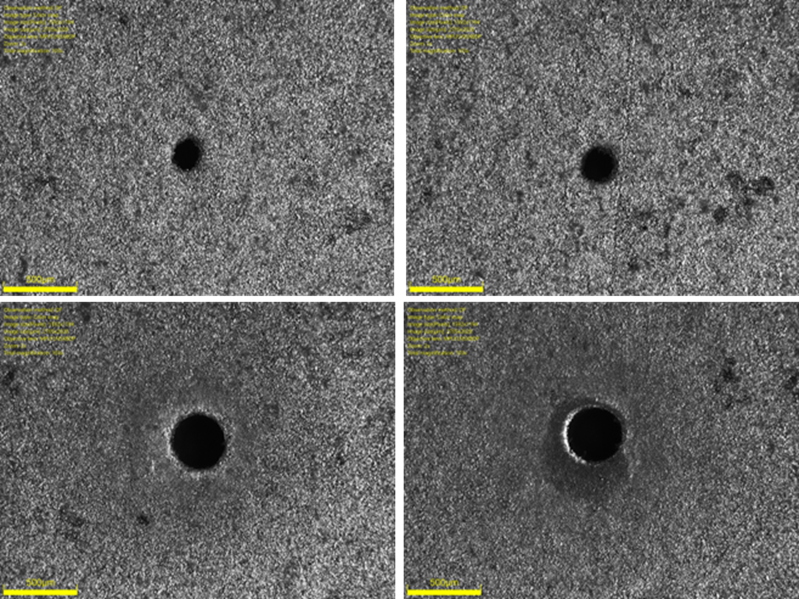
2. Fabrication of array of micro-tools
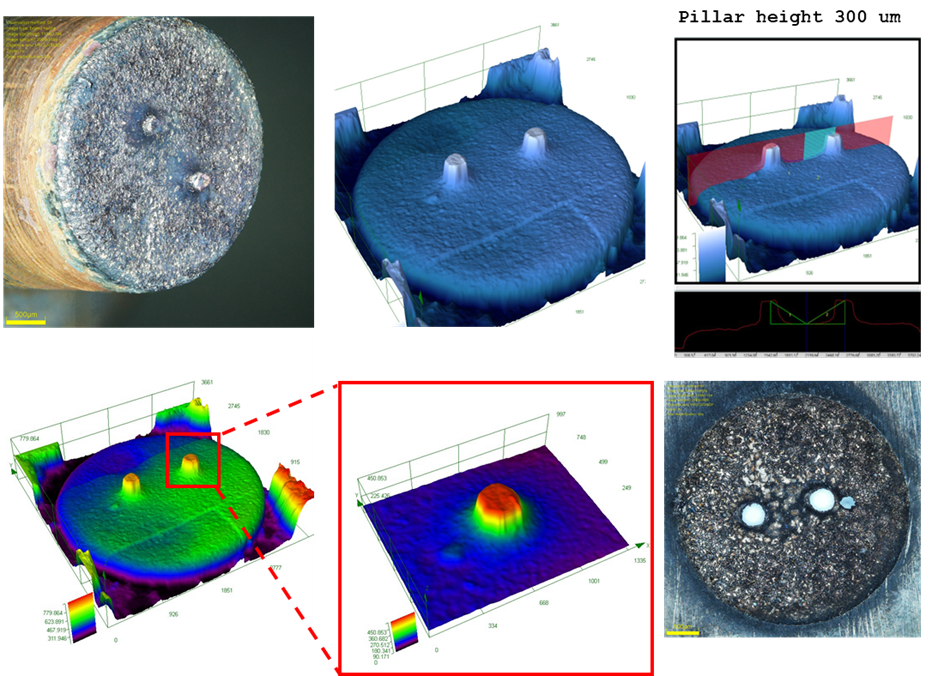
The EDM has successfully fabricated micro-pillars on copper alloy. The average height of the micro-pillars are around 300 um. This possibility has opened the doors to fabricate different varieties of micro-textured shapes on any conductive materials. Further, capable to extent to produce high aspect ratio micro-tools.
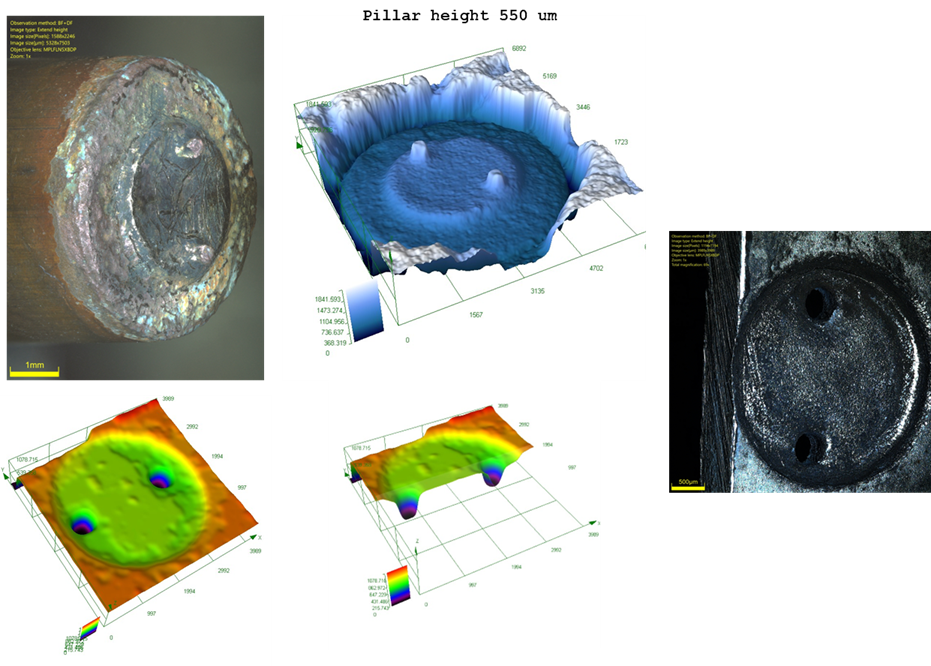
The EDM has successfully fabricated micro-pillars on copper alloy. The average height of the micro-pillars are around 550 um. Thus, micro-die can be fabricated for micro-mold applications. Further, due to low tool wear, we can facilitate to produce high aspect ratio micro-features.